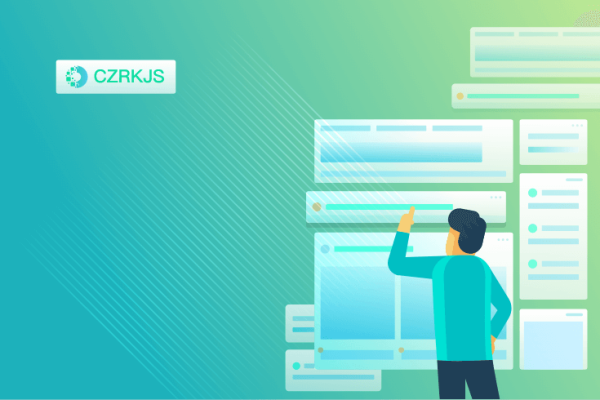
How Car Traction Control Systems Work
How Car Traction Control Systems Work: The Complete Guide to Maintaining Optimal Grip
Introduction to Traction Control Technology
In the constantly evolving world of automotive technology, traction control systems (TCS) stand as one of the most significant advancements in vehicle safety and performance. These sophisticated electronic systems work tirelessly behind the scenes to maintain optimal tire grip on the road surface, preventing dangerous wheel spin and helping drivers maintain control in challenging driving conditions. From rain-slicked highways to icy mountain passes, traction control serves as an invisible guardian, constantly monitoring and adjusting power delivery to keep your vehicle moving safely in the intended direction.
The development of traction control represents a major milestone in automotive engineering, bridging the gap between driver skill and technological assistance. While skilled drivers have always understood the importance of smooth throttle application, modern traction control systems can react to changing road conditions far faster than any human, making them invaluable for both everyday commuting and performance driving. This comprehensive guide will explore the intricate workings of traction control systems, their components, operation principles, and the remarkable benefits they provide to drivers worldwide.
The Physics Behind Traction: Understanding the Fundamentals
To fully appreciate how traction control systems work, we must first understand the fundamental physics of tire-road interaction. Traction, in automotive terms, refers to the friction between a vehicle’s tires and the road surface that allows for acceleration, braking, and cornering. This friction is governed by complex physical principles that traction control systems must constantly monitor and manage.
The coefficient of friction between tires and road varies dramatically depending on surface conditions. Dry asphalt offers excellent grip (coefficient around 0.7-0.9), while wet roads reduce this to about 0.4-0.6, and icy conditions can plummet to a dangerously low 0.1-0.2. Traction control systems must account for these variations in real-time, adjusting their interventions accordingly. When a tire loses traction, it begins to spin faster than the vehicle’s actual speed – this discrepancy is what traction control systems detect and correct.
Another critical concept is the traction circle, which illustrates how a tire’s available grip must be divided between acceleration, braking, and cornering forces. A tire can only provide maximum grip in one direction at a time – attempting to accelerate hard while cornering sharply, for example, may exceed the tire’s total available grip, leading to loss of control. Modern traction control systems understand these physical limits and help keep the vehicle operating within safe parameters.
Historical Development of Traction Control Systems
The journey of traction control technology began long before its widespread adoption in consumer vehicles. Early mechanical systems appeared in high-performance and racing applications as far back as the 1930s, but it wasn’t until the advent of electronic controls that traction management became practical for everyday vehicles.
Buick introduced the MaxTrac system in 1971, generally considered the first production electronic traction control. This primitive but innovative system used an early computer to detect rear wheel spin and retard ignition timing to reduce power. Throughout the 1980s, European manufacturers like BMW and Mercedes-Benz refined these systems, integrating them with emerging anti-lock brake technology.
The 1990s saw traction control become more sophisticated and widespread, with the introduction of wheel-speed sensors that could detect slip more accurately. By the early 2000s, traction control had become standard equipment on most mid-range and luxury vehicles, eventually trickling down to economy cars as the technology became more affordable to produce.
Modern systems represent the culmination of decades of refinement, now fully integrated with other vehicle stability systems and capable of remarkably precise interventions. Today’s traction control can differentiate between various types of road surfaces, adapt to different driving styles, and even anticipate loss of traction before it occurs using predictive algorithms.
Core Components of a Modern Traction Control System
A contemporary traction control system comprises several key components working in harmony to monitor and maintain optimal traction. Understanding these parts helps illuminate how the system functions as a whole.
Wheel Speed Sensors: These electromagnetic sensors, typically one at each wheel, continuously monitor the rotational speed of each tire. By comparing these speeds, the system can detect when one wheel is spinning faster than others (indicating loss of traction). Modern sensors can detect minute speed differences with remarkable accuracy.
Electronic Control Unit (ECU): The brain of the traction control system, this computer processes data from all sensors and determines when and how to intervene. Modern ECUs can make these calculations hundreds of times per second, ensuring near-instantaneous response to changing conditions.
Hydraulic Modulator: This component works with the braking system to apply precise brake pressure to individual wheels when needed. By braking a spinning wheel, the system can transfer torque to wheels with better traction, similar to how a limited-slip differential operates.
Throttle Control: Most modern systems can communicate with the engine control unit to reduce power by adjusting throttle position, fuel delivery, or ignition timing when excessive wheel spin is detected. Some performance-oriented systems can even cut specific cylinders to reduce power more precisely.
Yaw Rate and Steering Angle Sensors: These additional sensors help the system understand the driver’s intended direction, allowing more sophisticated interventions that consider both traction and vehicle stability.
These components work together seamlessly, often without the driver’s awareness, to maintain optimal traction in virtually all driving conditions.
How Traction Control Operates: Step-by-Step Process
The operation of a traction control system follows a precise sequence of detection, calculation, and intervention that occurs in fractions of a second. Here’s a detailed breakdown of the process:
- Continuous Monitoring: The system constantly compares rotational speeds of all wheels using data from wheel speed sensors. Under normal conditions, all wheels turn at roughly the same speed relative to the vehicle’s movement.
- Slip Detection: When a driver applies throttle (especially aggressively), one or more drive wheels may begin to spin faster than the vehicle’s actual speed. The system detects this discrepancy by comparing the spinning wheel’s speed to non-driven wheels or calculated vehicle speed.
- Intervention Decision: The ECU analyzes the degree of slip, vehicle speed, steering angle, and other factors to determine the appropriate response. The system may choose to apply brakes to the spinning wheel, reduce engine power, or employ a combination of both.
- Brake Application: If brake intervention is needed, the hydraulic modulator applies precise pressure to the brake caliper of the spinning wheel. This has two effects: it slows the spinning wheel directly, and it effectively transfers torque to the wheel(s) with better traction through the differential.
- Throttle Adjustment: Simultaneously or alternatively, the system may signal the engine control unit to reduce power. This can be achieved by closing the electronic throttle, retarding ignition timing, or in some systems, temporarily cutting fuel to specific cylinders.
- Stabilization: As traction is regained, the system gradually reduces its interventions, returning full control to the driver once normal operation is restored.
- System Reset: The system continuously monitors conditions, ready to intervene again if needed. Modern systems can make these adjustments hundreds of times per minute if necessary, providing seamless traction management.
This entire process occurs with such speed and precision that most drivers only notice the system’s operation through dashboard indicator lights or subtle changes in engine note and pedal response.
Different Types of Traction Control Systems
While all traction control systems share the same fundamental purpose, various implementations exist with different approaches to managing traction loss. Understanding these variations helps explain why different vehicles may handle similarly slippery conditions in distinct ways.
Brake-Based Systems: The most common type in passenger vehicles, these systems primarily use individual wheel braking to control traction. When a wheel spins, the system applies brake pressure to that wheel, which naturally transfers power to wheels with better grip through the differential. These systems are effective and relatively inexpensive to implement but can feel intrusive in performance driving situations.
Engine Management Systems: Some implementations focus primarily on reducing engine power when slip is detected. This approach is common in vehicles without sophisticated brake-based systems or as a secondary method in more advanced setups. While effective at preventing wheel spin, these systems can feel sluggish as they significantly reduce power output.
Combined Brake and Throttle Systems: Most modern vehicles use this integrated approach, combining the precision of brake application with the broader control of engine power reduction. These systems offer the most nuanced interventions and can adapt to a wider range of driving conditions.
Active Differential Systems: Found primarily in high-performance and all-wheel-drive vehicles, these advanced systems can actively vary torque distribution between wheels using electronically controlled differentials. When combined with traditional traction control methods, they provide exceptional grip and stability.
Predictive Traction Control: The cutting edge of traction management, these systems use additional sensors (like infrared road surface scanners) and predictive algorithms to anticipate traction loss before it occurs, allowing even smoother interventions.
Each type has its advantages and ideal applications, with more sophisticated systems generally offering better performance but at higher cost and complexity.
Traction Control vs. Stability Control: Understanding the Difference
While often mentioned together, traction control and electronic stability control (ESC) are distinct systems that serve complementary purposes. Understanding their differences clarifies how modern vehicles maintain control in challenging conditions.
Traction control specifically prevents wheel spin during acceleration, focusing on maintaining forward grip. Its primary concern is preventing the drive wheels from spinning faster than the vehicle’s actual speed, which is especially important when starting from rest or accelerating on slippery surfaces.
Electronic stability control, by contrast, addresses overall vehicle stability in various situations including cornering, braking, and evasive maneuvers. ESC uses many of the same sensors as traction control but adds yaw rate and lateral acceleration sensors to detect when the vehicle’s actual direction differs from the driver’s intended path (as indicated by steering wheel position). When such a discrepancy is detected, ESC can apply individual brakes and reduce engine power to help bring the vehicle back under control.
Most modern vehicles integrate these systems under a unified electronic stability program (ESP) that manages both traction and stability. However, some older or more basic vehicles may have traction control without full stability control. The integration allows for more sophisticated interventions – for example, the system might use traction control to prevent wheel spin during acceleration out of a corner while simultaneously using stability control to prevent oversteer or understeer.
Benefits of Traction Control Systems
The implementation of traction control technology has brought numerous benefits to vehicle safety, performance, and drivability. These advantages explain why traction control has become nearly universal in modern vehicles.
Enhanced Safety: By preventing wheel spin during acceleration, traction control helps maintain vehicle stability and prevents loss of control, particularly on slippery surfaces. This is especially valuable when accelerating from a stop on wet or icy roads, where uncontrolled wheel spin could lead to skidding or fishtailing.
Improved Acceleration: Contrary to some perceptions, properly calibrated traction control can actually improve acceleration in low-grip conditions by maximizing the available traction. Without traction control, aggressive throttle application often leads to excessive wheel spin that actually slows acceleration.
Increased Tire Life: By preventing wheel spin, traction control reduces unnecessary tire wear caused by spinning tires scrubbing against the road surface. This is particularly noticeable in high-torque vehicles that could easily break traction under power.
Better Performance in Adverse Conditions: Traction control proves invaluable in rain, snow, ice, gravel, and other low-traction situations where maintaining grip is challenging. It effectively augments driver skill, helping even inexperienced drivers navigate tricky conditions more safely.
Enhanced Driver Confidence: Knowing the vehicle will help maintain traction allows drivers to focus more on steering and situational awareness rather than constantly modulating throttle inputs to prevent wheel spin.
Support for Other Safety Systems: Traction control works synergistically with other vehicle safety systems like ABS and stability control, creating a comprehensive network of electronic safeguards.
These benefits have made traction control one of the most significant automotive safety advancements of recent decades, contributing to measurable reductions in accidents caused by loss of control.
Limitations and Considerations of Traction Control
While traction control systems offer substantial benefits, they are not infallible, and understanding their limitations is crucial for safe driving. No electronic system can overcome the fundamental laws of physics or replace prudent driving practices.
Physical Limits Remain: Traction control cannot create grip where none exists. On extremely slippery surfaces like glare ice or deep mud, even the most sophisticated system may be unable to prevent wheel spin or maintain forward motion.
Performance Trade-offs: Some systems, particularly older or more basic implementations, may feel intrusive during spirited driving, cutting power more aggressively than some drivers would prefer. This has led to the inclusion of traction control defeat switches in many performance-oriented vehicles.
System Response Time: While modern systems react remarkably quickly, there is always a slight delay between slip detection and intervention. In rapidly changing conditions, this can sometimes result in brief periods of wheel spin before the system responds.
Maintenance Requirements: Like all vehicle systems, traction control components require proper maintenance to function correctly. Faulty wheel speed sensors or other issues can impair system operation, sometimes without obvious symptoms until traction is needed.
Driver Overreliance: Perhaps the most significant limitation is the potential for drivers to overestimate the system’s capabilities, leading to riskier driving behaviors in poor conditions. Traction control is an aid, not a replacement for cautious driving appropriate to conditions.
Understanding these limitations helps drivers use traction control effectively while maintaining realistic expectations about its capabilities.
Traction Control in Different Driving Conditions
Traction control systems must adapt to a wide variety of road surfaces and driving scenarios. Modern systems can recognize different conditions and adjust their interventions accordingly, though the effectiveness varies by situation.
Wet Roads: On rain-slicked pavement, traction control prevents the common problem of wheel spin during acceleration from stops or when climbing hills. The system’s quick interventions help maintain forward momentum without excessive slipping.
Snow and Ice: In winter conditions, traction control proves particularly valuable, helping drivers accelerate smoothly on packed snow or ice. However, as mentioned earlier, there are limits to what it can accomplish on extremely slippery surfaces.
Loose Surfaces: On gravel, dirt, or sand, some systems may actually hinder progress by over-aggressively preventing wheel spin, which can sometimes help dig down to firmer surfaces. Many modern systems have special modes or reduced sensitivity for such conditions.
Performance Driving: On racetracks or during spirited driving, unrestricted wheel spin may sometimes be desirable for techniques like power-oversteer. This is why many performance cars allow partial or complete traction control deactivation.
Hill Starts: When starting on steep inclines, traction control prevents the wheel spin that often occurs as drivers apply extra throttle to prevent rolling backward.
Towing: When pulling heavy trailers, traction control helps manage the increased load on drive wheels, preventing spin that could lead to loss of control.
Understanding how traction control operates in these various scenarios helps drivers anticipate its behavior and use it most effectively.
Advanced Traction Control Features in Modern Vehicles
As automotive technology advances, traction control systems have incorporated increasingly sophisticated features that enhance their effectiveness and adaptability. These innovations represent the cutting edge of vehicle dynamics control.
Adaptive Traction Control: Some modern systems can learn driving patterns and road conditions, adjusting their intervention thresholds accordingly. For example, a system might become slightly more permissive if it detects consistent aggressive driving on dry pavement.
Cornering Traction Control: Advanced systems consider steering angle and lateral acceleration when managing traction, allowing for more nuanced interventions during cornering. This helps prevent both inside wheel spin and destabilizing power cuts mid-corner.
Launch Control: Primarily found in performance vehicles, this specialized traction control mode optimizes acceleration from a standstill, allowing maximum power without wheel spin for ideal straight-line performance.
Off-Road Modes: Many SUVs and trucks now feature specialized traction control calibrations for off-road use, which may allow more wheel spin when needed while still preventing complete loss of control.
Torque Vectoring: Some high-end systems can not only prevent wheel spin but actively distribute torque between wheels to enhance cornering performance and stability.
Predictive Systems: Using GPS, camera inputs, or other sensors, some experimental systems can anticipate low-traction areas (like shaded spots that might be icy) and prepare interventions before wheel spin occurs.
These advanced features demonstrate how traction control technology continues to evolve, becoming more sophisticated and situationally aware with each new generation of vehicles.
Maintenance and Troubleshooting of Traction Control Systems
Like all vehicle systems, traction control requires proper maintenance to function correctly. Understanding common issues and maintenance needs helps ensure the system remains operational when needed.
Common Issues:
- Faulty wheel speed sensors (a frequent cause of traction control warnings)
- Damaged or corroded wiring to sensors
- Problems with the hydraulic modulator or brake system
- Issues with the electronic control unit or its connections
- Discrepancies in tire size or pressure that confuse the system
Warning Signs:
- Illuminated traction control warning light
- System seems overly intrusive or not intervening when expected
- Related systems like ABS showing warnings
- Strange brake behavior during acceleration
Maintenance Tips:
- Regularly inspect and clean wheel speed sensors (especially important in areas with winter road treatments)
- Ensure all tires are properly inflated and of matching size/wear
- Address any ABS or brake system warnings promptly, as these systems are interconnected
- Have the system scanned for codes if warning lights appear, even if no obvious symptoms exist
Professional Service:
While some basic maintenance can be performed by owners, most traction control system repairs require professional diagnosis and specialized equipment. Modern systems are complex and often integrated with other vehicle systems, making DIY repairs challenging.
Proper maintenance ensures the traction control system will be ready to perform when needed, maintaining its critical safety function.
The Future of Traction Control Technology
As vehicle technology continues its rapid advancement, traction control systems are poised to become even more sophisticated and integrated with other vehicle systems. Several emerging trends point to the future direction of this critical safety technology.
Integration with Autonomous Driving: As self-driving technology develops, traction control will become more tightly integrated with autonomous systems, providing seamless control in all conditions without human intervention.
Vehicle-to-Everything (V2X) Communication: Future systems may receive real-time road condition data from other vehicles or infrastructure, allowing preemptive traction adjustments before encountering slippery surfaces.
Artificial Intelligence: Machine learning algorithms could enable systems to adapt more precisely to individual driving styles and predict traction loss with greater accuracy.
Enhanced Sensor Suites: Additional sensors like road surface scanners, moisture detectors, and temperature sensors could provide more comprehensive data for traction calculations.
Electrified Drivetrains: In electric vehicles, instant torque control at each individual wheel (in some cases even without traditional braking intervention) could allow for incredibly precise traction management.
Cloud-Based Adjustments: Systems might download traction control calibrations specific to current weather and road conditions in the vehicle’s location.
These advancements promise to make traction control even more effective and transparent to drivers, further enhancing vehicle safety and performance in all conditions.
Conclusion: The Essential Role of Traction Control in Modern Driving
From its early mechanical beginnings to today’s sophisticated electronic systems, traction control technology has become an indispensable component of vehicle safety and performance. By constantly monitoring wheel speeds and making instantaneous adjustments to braking and power delivery, these systems help drivers maintain control in conditions that might otherwise lead to dangerous loss of traction.
While not a substitute for careful driving appropriate to conditions, traction control provides an invaluable safety net that has prevented countless accidents and helped drivers navigate challenging situations with greater confidence. As the technology continues to evolve alongside other automotive advancements, we can expect traction control systems to become even more seamless and effective, further enhancing their role in keeping drivers safe on the road.
Understanding how these systems work not only satisfies technical curiosity but also helps drivers use them more effectively, recognizing both their capabilities and limitations. In an era of rapid automotive technological advancement, traction control stands as one of the most significant and universally beneficial innovations, quietly working in the background to make every journey safer.