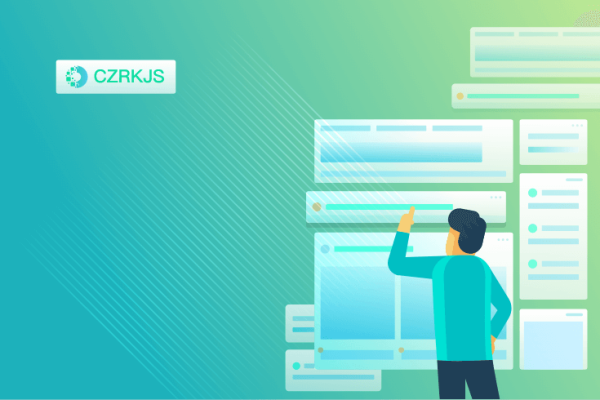
How Car Throttle Bodies Work
How Car Throttle Bodies Work: The Complete Guide to Engine Airflow Control
The throttle body is one of the most critical components in your vehicle’s engine management system, serving as the gateway that regulates airflow into the combustion chambers. This comprehensive guide will explore the intricate workings of throttle bodies, their evolution through automotive history, different types available today, and their vital role in engine performance and efficiency.
The Fundamentals of Throttle Body Operation
At its core, a throttle body is a butterfly valve that controls the amount of air entering an engine’s intake manifold. When you press the accelerator pedal, you’re not directly increasing fuel flow as many believe—you’re actually commanding the throttle plate to open wider, allowing more air into the engine. This action triggers the engine control unit (ECU) to increase fuel injection accordingly, maintaining the optimal air-fuel ratio for combustion.
The basic components of a throttle body include:
- Throttle plate (butterfly valve): A flat, circular metal disc mounted on a rotating shaft
- Throttle shaft: The axle that allows the plate to pivot
- Throttle position sensor (TPS): Monitors how far the throttle is open
- Idle air control valve (IAC): Manages idle speed (in older systems)
- Housing: The aluminum or composite body that contains all components
Modern throttle bodies are marvels of precision engineering, with tolerances measured in thousandths of an inch to ensure smooth operation and accurate airflow measurement. The housing is carefully designed to minimize turbulence as air rushes through at speeds that can exceed 100 mph in high-performance engines at wide-open throttle.
Historical Evolution of Throttle Technology
The concept of throttle control dates back to the earliest internal combustion engines. In carbureted engines (common until the 1980s), the throttle body was integrated into the carburetor assembly. These mechanical systems used cables and linkages that directly connected the accelerator pedal to the throttle plate—a simple but effective design that lacked precision.
The introduction of electronic fuel injection in the late 1970s marked a significant advancement. Early fuel injection systems still used mechanical throttle bodies with cables, but by the mid-1990s, automakers began adopting electronic throttle control (ETC), also known as “drive-by-wire” systems. This revolutionary approach eliminated the physical cable connection between pedal and throttle, instead using sensors and electric motors for control.
Modern ETC systems provide several advantages:
- More precise throttle response
- Integration with traction and stability control systems
- Ability to implement cruise control and automatic engine speed management
- Reduced mechanical complexity under the hood
Types of Throttle Bodies in Modern Vehicles
Today’s automotive market features several throttle body designs, each with specific applications and performance characteristics:
1. Single-Bore Throttle Bodies
The most common design for standard passenger vehicles, featuring a single butterfly valve. These are cost-effective and reliable, sized appropriately for the engine’s airflow requirements. Most four- and six-cylinder engines use this configuration.
2. Dual-Bore Throttle Bodies
Used in some V6 and V8 applications, these feature two smaller butterfly valves operating in tandem rather than one large valve. This design improves throttle response at lower RPMs while still allowing sufficient airflow at high RPMs.
3. Electronic Throttle Bodies (Drive-by-Wire)
The current industry standard, these use electric motors to open and close the throttle plate based on electronic signals from the accelerator pedal position sensor. They allow for advanced engine management features but are more complex than mechanical systems.
4. Cable-Driven Throttle Bodies
Still found in some performance applications and older vehicles, these use a physical cable connection between the accelerator pedal and throttle plate. Preferred by some enthusiasts for their direct feel, though less precise than electronic systems.
5. Performance Throttle Bodies
Aftermarket units designed for high-performance applications, featuring larger diameters (often 70mm+), smoother airflow paths, and sometimes multiple plates. These can increase horsepower when properly matched to other engine modifications.
The Science Behind Throttle Body Sizing
Selecting the proper throttle body size involves careful engineering calculations. While it might seem that a larger throttle body always means better performance, this isn’t necessarily true. The relationship between throttle body diameter and engine performance follows these principles:
- Airflow Velocity: A properly sized throttle body maintains optimal air velocity. Too large, and air speed drops, reducing throttle response at lower RPMs. Too small, and airflow becomes restricted at higher RPMs.
-
Engine Displacement Relationship: As a general rule, throttle body diameter (in millimeters) should roughly equal engine displacement in liters multiplied by 25. For example:
- 2.0L engine: ~50mm throttle body
- 5.0L engine: ~75mm throttle body
- Volumetric Efficiency: High-performance engines with improved breathing (better cylinder heads, cams, etc.) can benefit from slightly larger throttle bodies as they can move more air.
- Forced Induction Considerations: Turbocharged and supercharged engines often use larger throttle bodies since the forced induction system can overcome some of the low-RPM velocity issues.
Automotive engineers use computational fluid dynamics (CFD) software to model airflow through throttle bodies, optimizing the shape of the bore, throttle plate, and shaft to minimize turbulence and pressure drops.
Electronic Throttle Control: How Modern Systems Work
Drive-by-wire systems represent the cutting edge of throttle technology. Here’s a detailed look at their operation:
- Pedal Position Sensors: When you press the accelerator, two or three redundant sensors measure pedal angle and send signals to the ECU.
-
ECU Processing: The engine computer evaluates multiple parameters including:
- Current engine speed
- Vehicle speed
- Transmission gear
- Traction control status
- Cruise control inputs
- Engine temperature
- Throttle Motor Activation: Based on these inputs, the ECU sends commands to a small but powerful electric motor in the throttle body.
- Throttle Plate Movement: The motor rotates the throttle shaft through a gear reduction system, providing precise control over plate angle.
- Feedback Loop: The throttle position sensor continuously reports actual throttle angle back to the ECU, allowing for real-time adjustments.
This system allows for features like:
- Rev matching in manual transmission vehicles
- Torque management to protect drivetrain components
- Traction control integration where the ECU can reduce throttle during wheel slip
- Adaptive cruise control that maintains set following distances
Throttle Body Maintenance and Common Issues
Like all mechanical components, throttle bodies require periodic attention to maintain optimal performance. Common symptoms of throttle body problems include:
- Rough idle or stalling
- Poor acceleration response
- Illuminated check engine light (often P0121-P0123 or P0221-P0223 throttle position codes)
- Surging or inconsistent engine speed
- Reduced fuel economy
Cleaning Procedures
Carbon buildup is the throttle body’s primary enemy. A proper cleaning involves:
- Removing the air intake duct
- Using throttle body cleaner (never carburetor cleaner, which can damage coatings)
- Gently wiping the bore and plate with a soft cloth
- Cleaning the edges where the plate meets the bore
- Inspecting the shaft for excessive play
- Reassembling and performing an idle relearn procedure if necessary
Common Failure Points
- Throttle Position Sensor (TPS): Worn sensors provide inaccurate readings
- Idle Air Control Valve (in older models): Can stick or fail
- Carbon Buildup: Especially in direct injection engines where fuel doesn’t clean the intake tract
- Motor Failure (in electronic units): Rare but possible
- Shaft Wear: Leads to air leaks around the throttle plate
Performance Upgrades and Tuning Considerations
For enthusiasts looking to maximize their engine’s potential, throttle body upgrades can offer noticeable improvements when done correctly:
Aftermarket Options
- Larger Diameter Units: Typically increase by 10-15% over stock
- Bored/Port-matched Stock Units: Cost-effective improvement
- High-Flow Designs: Feature knife-edged shafts and optimized airflow paths
Tuning Requirements
Modern ECUs must be reprogrammed after throttle body upgrades to account for:
- Changed airflow characteristics
- Revised throttle position sensor calibration
- Adjusted torque management tables
Realistic Expectations
While throttle body upgrades can provide 5-15 horsepower on modified engines, they rarely show significant gains on stock engines where the factory unit is already properly sized. The best results come when combined with other intake system improvements like cold air intakes, performance manifolds, and tuned exhaust systems.
The Future of Throttle Technology
As automotive engineering continues to evolve, several emerging technologies may change how we control engine airflow:
- Integrated Throttle/Manifold Assemblies: Combining functions into single modules
- Active Aerodynamics: Variable geometry throttle bodies that change shape based on demand
- Predictive Control Systems: Using GPS and AI to anticipate throttle needs
- Hybrid/Electric Integration: Throttle bodies working in concert with electric motor torque delivery
Some experimental designs even eliminate the traditional butterfly valve altogether, using variable intake runner lengths or other methods to control engine airflow without the pumping losses associated with conventional throttle bodies.
Conclusion: The Critical Role of Throttle Bodies in Modern Motoring
From simple mechanical flaps to sophisticated electronic control modules, throttle bodies have evolved into precision instruments that balance engine performance, fuel efficiency, and emissions control. Understanding their operation provides insight into the complex interplay of components that make modern engines so responsive and efficient.
Whether you’re a casual driver interested in how your vehicle works or a performance enthusiast looking to optimize your setup, appreciating the throttle body’s role in engine operation is fundamental. Proper maintenance and, when appropriate, well-considered upgrades can keep your engine breathing freely for years of reliable service.
As automotive technology continues advancing, the humble throttle body will undoubtedly evolve further, but its essential function—regulating the vital flow of air that makes internal combustion possible—will remain central to engine operation for the foreseeable future.