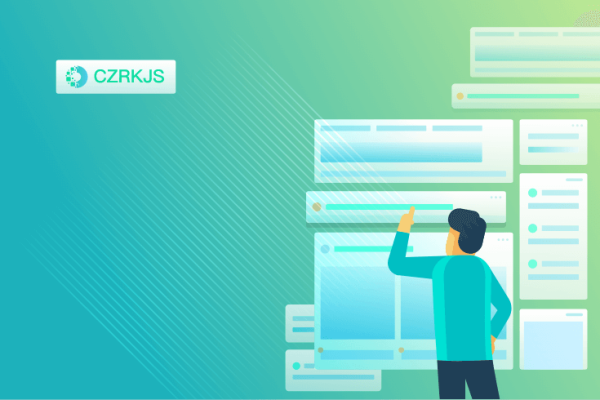
How Car Load-Adaptive Cruise Control Works
How Car Load-Adaptive Cruise Control Works: The Intelligent Driving Revolution
In the ever-evolving landscape of automotive technology, adaptive cruise control (ACC) has emerged as one of the most transformative features in modern vehicles. However, the latest innovation—load-adaptive cruise control—takes this technology to unprecedented levels of sophistication. This comprehensive guide explores the intricate workings of load-adaptive cruise control systems, their components, benefits, and the remarkable engineering that makes them possible.
The Evolution of Cruise Control: From Basic to Load-Adaptive
The journey of cruise control began in 1948 when inventor Ralph Teetor developed the first speed control system for automobiles. These primitive systems maintained a constant speed set by the driver but required manual adjustment when encountering traffic or terrain changes. The advent of radar-based adaptive cruise control in the 1990s marked a significant leap forward, allowing vehicles to automatically adjust speed based on traffic conditions.
Load-adaptive cruise control represents the next evolutionary step—a system that doesn’t just respond to external traffic conditions but also accounts for the vehicle’s internal state. By considering factors like passenger count, cargo weight, trailer load, and even fuel levels, these intelligent systems optimize performance, safety, and efficiency in ways traditional ACC never could.
Core Components of Load-Adaptive Cruise Control Systems
1. Advanced Sensor Array
Modern load-adaptive systems integrate multiple sensor technologies:
- Radar sensors (typically 77GHz) provide long-range detection (up to 200 meters) of vehicles ahead
- LiDAR sensors offer high-resolution 3D mapping of the vehicle’s surroundings
- Ultrasonic sensors assist with close-range detection during low-speed operation
- Stereo cameras with advanced image processing identify vehicles, pedestrians, and road features
- Load sensors in the suspension system measure weight distribution and vehicle mass
2. Vehicle Dynamics Monitoring System
This subsystem continuously analyzes:
- Suspension compression at each wheel
- Powertrain load through engine control unit (ECU) data
- Brake system pressure requirements
- Transmission shift patterns and torque converter behavior
- Fuel consumption rates relative to speed and acceleration
3. Central Processing Unit
The brain of the system features:
- High-performance multi-core processors
- Machine learning algorithms trained on millions of driving scenarios
- Predictive modeling capabilities that anticipate load changes
- Integration with other vehicle systems (stability control, traction control, etc.)
4. Actuation Systems
These components execute the system’s commands:
- Electronic throttle control for precise acceleration management
- Adaptive transmission programming for optimal gear selection
- Brake-by-wire systems for smooth deceleration
- Trailer sway control when towing heavy loads
How Load-Adaptive Cruise Control Operates
Initialization and Calibration
When activated, the system undergoes a sophisticated calibration process:
- Load Assessment: The system measures suspension compression at each wheel to calculate total vehicle mass and weight distribution.
- Performance Profiling: Based on the load measurement, the system creates a dynamic performance profile accounting for acceleration capability, braking distance, and cornering stability.
- Environmental Scanning: Sensors establish a 360-degree model of the vehicle’s surroundings, identifying lane markings, nearby vehicles, and potential obstacles.
- Driver Preference Integration: The system recalls stored driver preferences for following distance, acceleration aggressiveness, and other customizable parameters.
Real-Time Operation
During driving, the system performs continuous calculations:
- Target Vehicle Tracking: The primary radar tracks the speed and distance of vehicles ahead, while secondary sensors monitor adjacent lanes for potential cut-ins.
-
Load-Compensated Following Distance: Unlike conventional ACC that uses fixed distance settings, load-adaptive systems dynamically adjust following distance based on:
- Current vehicle mass (heavier vehicles require longer stopping distances)
- Road gradient (accounting for both uphill and downhill effects)
- Trailer presence and tongue weight
- Tire condition and brake pad wear (estimated through performance history)
-
Predictive Acceleration/Deceleration: The system anticipates speed changes required to maintain smooth operation:
- Gradual acceleration when heavily loaded to prevent excessive fuel consumption
- Earlier initiation of braking when towing to account for increased momentum
- Compensated throttle response when climbing hills with heavy loads
-
Curve Speed Adaptation: Using navigation data and camera input, the system adjusts speed before curves based on:
- Vehicle center of gravity (affected by roof loads or trailer towing)
- Suspension load distribution (preventing uneven weight transfer)
- Current road conditions (wet, dry, icy—detected through wheel slip monitoring)
Special Load Scenarios
The system intelligently adapts to various loading conditions:
-
Trailer Towing Mode:
- Automatically detects trailer connection through electrical coupling and camera recognition
- Adjusts following distance by up to 40% compared to unloaded operation
- Modifies lane change behavior to account for trailer length
- Activates trailer sway mitigation through subtle brake applications
-
Passenger/Cargo Loading:
- Recognizes seating occupancy through seat sensors or interior cameras
- Accounts for roof rack loads through suspension monitoring and optional height sensors
- Adjusts climate control priorities based on passenger distribution
-
Fuel Load Considerations:
- Tracks fuel consumption and tank level to predict decreasing vehicle mass
- Gradually modifies performance parameters as fuel burns off during long trips
- For electric vehicles, accounts for battery weight reduction as charge depletes
Technical Advantages Over Conventional ACC
1. Enhanced Safety
Load-adaptive systems provide significant safety improvements:
- Accurate Stopping Distance Calculation: By knowing the exact vehicle mass, the system can initiate braking precisely when needed, preventing late braking scenarios with heavy loads.
- Rollover Prevention: The system monitors weight distribution and can reduce speed proactively when high center-of-gravity loads (like roof cargo) might cause instability.
- Trailer Sway Mitigation: Early detection of trailer oscillation allows corrective action before the driver might notice a problem.
2. Improved Efficiency
The load awareness enables optimized performance:
- Adaptive Gear Selection: Transmission programming adjusts shift points based on load, preventing excessive revving or lugging.
- Predictive Energy Management: Hybrid and electric vehicles can optimize battery usage based on current load requirements.
- Fuel-Saving Strategies: The system learns driving patterns with various loads and suggests optimal speeds for fuel efficiency.
3. Comfort Optimization
By accounting for load, the system provides smoother operation:
- Gradual Acceleration: Prevents jerky starts when heavily loaded by moderating throttle application.
- Anticipatory Braking: Begins deceleration earlier when stopping heavy loads, creating a more comfortable experience.
- Curve Comfort: Speed adjustment before turns accounts for passenger comfort, not just vehicle stability.
Integration with Other Advanced Driver Assistance Systems (ADAS)
Modern load-adaptive cruise control doesn’t operate in isolation but works synergistically with other vehicle systems:
- Lane Keeping Assist: The system considers load when determining appropriate steering inputs, applying more assistance when towing or carrying heavy loads.
- Automatic Emergency Braking: Load data improves collision prediction algorithms, triggering interventions at precisely the right moment.
- Blind Spot Monitoring: When towing, the system extends monitoring ranges to account for trailer length.
- Crosswind Compensation: Uses load distribution data to better resist wind gusts, especially important for tall vehicles or those with roof loads.
- Hill Descent Control: Integrates load information to maintain optimal speed when going downhill with heavy loads.
The Role of Artificial Intelligence and Machine Learning
Modern load-adaptive cruise systems employ sophisticated AI techniques:
- Neural Networks: Process sensor data to identify patterns and predict vehicle behavior under various load conditions.
- Deep Learning: Continuously improves performance by analyzing thousands of real-world driving scenarios.
- Predictive Algorithms: Anticipate load changes based on driving patterns (e.g., recognizing when a frequently used vehicle is likely to be heavily loaded).
- Driver Profiling: Learn individual driving styles and adjust load compensation accordingly.
Future Developments in Load-Adaptive Technology
The next generation of systems promises even greater capabilities:
- Cloud-Based Load Profiles: Vehicles could download performance data for specific trailer models or common load configurations.
- Smart Cargo Recognition: Camera systems may identify and categorize loaded items to predict their effect on vehicle dynamics.
- Dynamic Load Monitoring: Continuous weight measurement during transit could account for shifting cargo or passenger movement.
- Platooning Integration: Heavy vehicles could coordinate braking and acceleration based on mutual load conditions when traveling in convoy.
- Predictive Load Routing: Navigation systems might suggest routes optimized for current load conditions, avoiding steep grades or sharp curves when heavily loaded.
Implementation Challenges and Solutions
Developing effective load-adaptive systems presents unique engineering challenges:
-
Sensor Accuracy: Requires precise load measurement technology that works consistently across all road conditions and vehicle ages.
- Solution: Multi-sensor fusion approaches that cross-validate data from suspension, powertrain, and dedicated load cells.
-
Computational Demands: Real-time load calculations require significant processing power.
- Solution: Dedicated AI accelerators in vehicle ECUs optimized for these specific calculations.
-
Driver Trust: Users must understand and accept the system’s load-based decisions.
- Solution: Clear HUD displays showing how load affects system behavior and optional override capabilities.
-
Aftermarket Compatibility: Systems must work with various trailer types and aftermarket modifications.
- Solution: Standardized trailer interfaces and learning modes that adapt to non-standard configurations.
Comparative Analysis: Load-Adaptive vs. Conventional ACC
Feature | Conventional ACC | Load-Adaptive ACC |
---|---|---|
Following Distance | Fixed or speed-based | Dynamically adjusted based on load |
Acceleration Profile | Standard curve | Load-optimized curve |
Braking Initiation | Reactive | Predictive based on mass |
Curve Handling | Basic speed reduction | Load-compensated stability control |
Towing Performance | Generic adjustment | Trailer-specific optimization |
Fuel Efficiency | Moderate improvement | Significant load-based optimization |
Safety Margin | Static | Dynamic based on current stability |
Real-World Applications and User Benefits
Drivers experience tangible improvements across various scenarios:
- Family Road Trips: The system automatically adjusts for full passenger loads and rooftop cargo carriers, providing smoother acceleration and more confident braking.
- Towing Applications: Boat and trailer owners benefit from optimized speed control that accounts for the trailer’s specific characteristics.
- Commercial Use: Delivery vehicles with variable cargo loads maintain consistent performance throughout the day as weight changes.
- Ride Sharing: Vehicles that frequently carry varying numbers of passengers adapt seamlessly to different loading conditions.
- Mountain Driving: The system perfectly compensates for both uphill and downhill grades while accounting for current load.
Maintenance and Calibration Considerations
To maintain optimal performance:
- Suspension Checks: Worn suspension components can affect load measurements—regular inspections are recommended.
- Sensor Calibration: Following significant repairs or modifications, system recalibration may be necessary.
- Software Updates: Manufacturers periodically release improvements to load calculation algorithms.
- Trailer Profile Updates: When using new trailers, allowing the system to learn their characteristics improves performance.
The Environmental Impact
Load-adaptive systems contribute to sustainability:
- Reduced Fuel Consumption: Optimized acceleration and speed maintenance can improve mileage by 5-15% depending on load conditions.
- Extended Component Life: By preventing excessive strain when heavily loaded, the system reduces wear on drivetrain components.
- Emission Reduction: More efficient operation translates to lower CO2 output, especially important for commercial fleets.
- Tire Preservation: Proper load management prevents uneven tire wear from improper weight distribution.
Conclusion: The Future of Intelligent Speed Control
Load-adaptive cruise control represents a significant milestone in automotive technology—one that acknowledges that a vehicle’s performance envelope changes dramatically based on how it’s being used. By integrating real-time load awareness into speed control algorithms, these systems provide safer, more efficient, and more comfortable driving experiences across the full spectrum of vehicle loading conditions.
As the technology continues to evolve, we can expect even deeper integration with other vehicle systems, more sophisticated predictive capabilities, and eventually, fully autonomous operation that perfectly accounts for both internal and external factors. The road ahead for adaptive cruise technology is one where vehicles don’t just respond to their environment, but fully understand their own capabilities within that environment—creating a new standard for intelligent transportation.