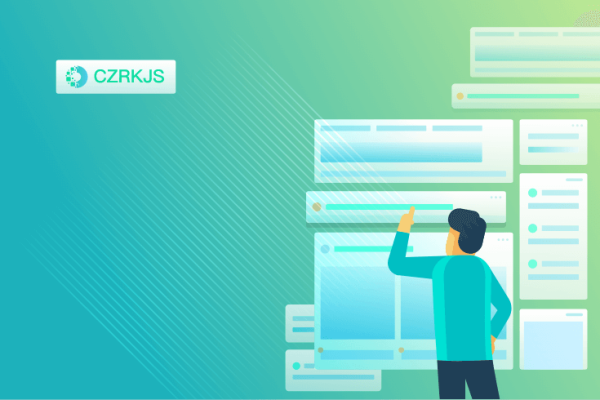
How 3D Printing Could Change Car Manufacturing
How 3D Printing Could Change Car Manufacturing
Introduction
The automotive industry has always been at the forefront of technological innovation, from the assembly line revolution pioneered by Henry Ford to the rise of electric vehicles (EVs) in the 21st century. Now, another groundbreaking technology is poised to transform car manufacturing: 3D printing, also known as additive manufacturing.
Unlike traditional manufacturing, which relies on subtractive processes (cutting, drilling, and milling materials), 3D printing builds objects layer by layer from digital models. This method offers unprecedented flexibility, efficiency, and customization potential. As automakers explore its applications, 3D printing could fundamentally alter how cars are designed, produced, and even repaired.
In this article, we will explore:
- The current state of 3D printing in automotive manufacturing
- Key advantages over conventional methods
- Real-world applications by leading car manufacturers
- Challenges and limitations
- The future of 3D-printed cars
The Current State of 3D Printing in Automotive Manufacturing
While 3D printing has been used in prototyping for years, its role in full-scale production is still evolving. Major automakers like BMW, Ford, and General Motors have integrated 3D printing for parts such as brackets, interior components, and even engine parts. Meanwhile, startups like Divergent 3D and Local Motors are pushing boundaries by creating almost entirely 3D-printed vehicles.
Prototyping & Tooling
One of the earliest uses of 3D printing in the automotive sector was rapid prototyping. Engineers can quickly produce scale models of new parts, test them, and refine designs without expensive tooling. This drastically reduces development time.
Additionally, custom tooling (jigs, fixtures, and molds) can be 3D printed on demand, saving costs compared to traditional machining.
End-Use Parts
More recently, automakers have begun using 3D printing for final production parts. Examples include:
- BMW’s i8 Roadster – Features a 3D-printed convertible roof bracket
- Bugatti’s Chiron – Uses 3D-printed titanium brake calipers
- Porsche’s Classic Division – Restores rare vintage cars with 3D-printed components
Key Advantages of 3D Printing in Car Manufacturing
1. Design Freedom & Lightweighting
Traditional manufacturing imposes constraints due to machining limitations. In contrast, 3D printing allows for complex geometries that were previously impossible, such as hollow structures, lattice designs, and organic shapes.
This enables lightweighting—reducing vehicle weight without sacrificing strength. Lighter cars improve fuel efficiency and battery range in EVs.
2. Mass Customization
Consumers increasingly demand personalized vehicles. 3D printing makes it economically viable to produce custom interiors, bespoke trim pieces, and even one-off body panels without retooling entire production lines.
3. Reduced Waste & Sustainable Manufacturing
Additive manufacturing generates far less material waste than subtractive methods. Some companies even use recycled plastics and metals, making production more sustainable.
4. Supply Chain Simplification
Instead of storing thousands of spare parts, automakers could print components on demand, reducing inventory costs and logistics complexity. This is particularly useful for low-volume or discontinued models.
Real-World Applications
Local Motors & the Olli Autonomous Shuttle
Local Motors made headlines with Olli, a self-driving shuttle with a mostly 3D-printed body. The company uses direct metal laser sintering (DMLS) and large-format polymer printing to create modular designs that can be updated rapidly.
Divergent 3D’s Blade Supercar
Divergent 3D’s Blade supercar features a 3D-printed aluminum chassis that is lighter and stronger than traditional frames. Their approach could revolutionize car manufacturing by reducing factory footprints and energy consumption.
Ford’s 3D-Printed Brake Parts
Ford has integrated 3D-printed brake components in its performance vehicles, cutting weight while maintaining durability. The company also uses AI-driven generative design to optimize parts before printing.
Challenges & Limitations
Despite its promise, 3D printing faces hurdles before becoming mainstream in car production:
1. Speed & Scalability
Most industrial 3D printers are still too slow for mass production. While they excel at prototyping and low-volume parts, high-speed sintering and multi-laser systems are being developed to address this.
2. Material Limitations
While plastics and some metals are widely used, high-strength automotive alloys (like certain steels) remain difficult to print reliably. Research into new composite materials is ongoing.
3. Cost of Industrial Printers
Large-scale 3D printers capable of automotive-grade parts are expensive, though costs are decreasing as adoption grows.
4. Certification & Safety Standards
Regulatory bodies like the NHTSA and EU safety agencies must establish new testing protocols for 3D-printed car parts to ensure they meet crash safety standards.
The Future of 3D-Printed Cars
Looking ahead, several trends suggest 3D printing will play a major role in the automotive industry:
1. Hybrid Manufacturing
Rather than replacing traditional methods entirely, hybrid production lines (combining 3D printing with CNC machining and stamping) will likely emerge.
2. On-Demand Spare Parts
Dealerships and repair shops could print replacement parts locally, eliminating long wait times for rare components.
3. Fully 3D-Printed Vehicles
Companies like XEV and Czinger are working toward entirely 3D-printed cars, potentially reducing production costs by up to 60%.
4. AI-Optimized Designs
Generative design software, powered by AI, will create ultra-efficient structures that can only be manufactured via 3D printing.
Conclusion
3D printing is not just a futuristic concept—it is already reshaping car manufacturing. From lightweighting and customization to supply chain efficiency, the benefits are undeniable. While challenges remain, continued advancements in speed, materials, and certification will likely make additive manufacturing a cornerstone of the automotive industry.
In the coming decade, we may see factories with fewer assembly lines and more 3D printers, enabling faster innovation and greener production. The era of truly personalized, on-demand vehicles is closer than we think—and 3D printing is leading the charge.
Would you drive a 3D-printed car? The answer may soon be: “You already are.”